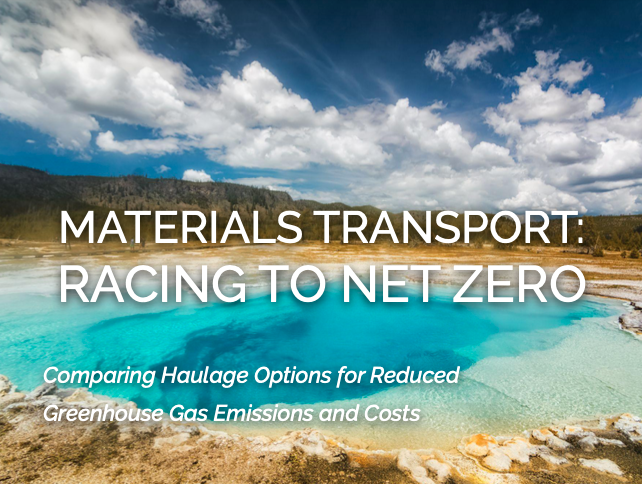
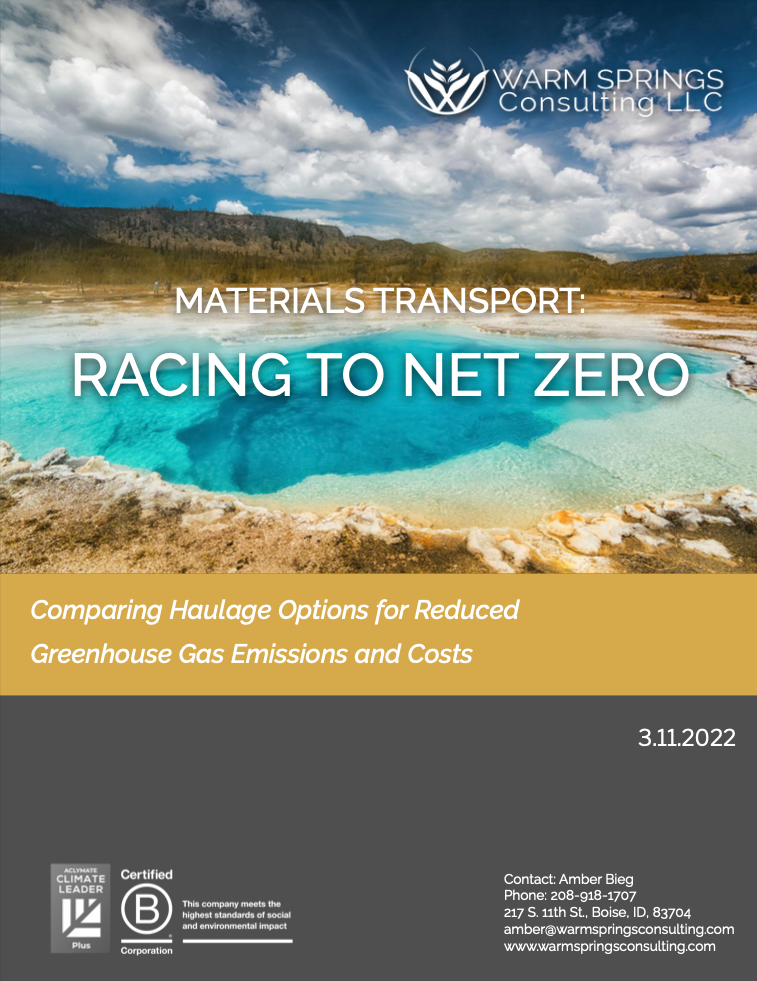
Comparing Haulage Options For Reduced Greenhouse Gas Emissions and Costs
Authors: Amber Bieg, M.B.A; Mitch Samson, I.E.S.E. M.B.A, B.S.M.E.; Zach Bell, B.A.; Jay Schuyler, B.A., and Austin Zinsser, M.S., P.G.
Keywords: Energy Transition | Electric Mining | Electricity Supply | Sustainability
Sign up for our email list to stay tuned for upcoming webinars and presentations about this study.
As the world progresses toward the renewable energy transition, the demand for minerals increases exponentially. According to the International Energy Agency (IEA) 2021 Net Zero by 2050 Report, critical mineral production needs to grow six times in order to combat climate change. It’s estimated that four to seven percent of global greenhouse gas (GHG) emissions come from the mining sector’s Scope 1 and 2 (direct and indirect) emissions. Including Scope 3 (upstream, downstream, and embedded) emissions, the sector accounts for 28% of global GHG emissions.
In a typical mining operation, diesel fuel is the biggest source of direct GHG emissions, and haulage is often the main source of diesel emissions. If a mine can electrify its hauling operations, it can significantly reduce GHG emissions and lower costs. Large haul trucks have been the industry standard for over 50 years and offer flexibility, relatively low capital cost (especially with equipment lease options), and guaranteed technology with known maintenance. The challenge will be to justify their continued use when there are more economical options that lead to significant reductions in GHG emissions.
Study Purpose
The purpose of this study is to compare seven haulage options in terms of greenhouse gas emissions (GHG), using the methodology defined by the Greenhouse Gas Protocol Scopes 1, 2, and 3 (Category 2). Additionally, this analysis compares operating and capital costs associated with the seven haulage options (both emerging and proven technologies): 1) Diesel-Electric Haul Trucks, 2) Battery-Electric Haul Trucks, 3) Fuel Cell Haul Trucks, 4) Railveyor, 5) Diesel-Electric Heavy Rail, 6) Long Haul Diesel Trucks, and 7) Conveyor. This analysis looks at both the emissions and costs associated with operating the equipment (fuel and electricity), the embedded emissions and costs associated with the construction and installation of the equipment itself, and the associated infrastructure (roads, powerlines, and rail). This study also compares these haulage systems in a hypothetical scenario as well as two real-world scenarios where mines have developed tradeoff studies specific to their sites. While this analysis focuses on mining operations, the energy and emissions factors can be applied to haulage for other industries. The agricultural sector uses much of the same equipment and this study could inform ag sector haulage as well.
Emissions and Costs
Diesel-electric haul trucks are estimated to have the highest GHG emissions of the specified hauling methods at 0.096 kilograms CO2e /tonne-km. This is directly related to the high emissions factor of diesel fuel and limited haul capacity per truck. The hauling method with the lowest emissions is the Railveyor system, with an estimated 0.012 kilograms CO2e /tonne-km.
Based on average diesel and electricity prices, the hauling method with the highest fuel operating cost is estimated to be diesel-electric haul trucks at $0.043 /tonne-km. Railveyor is estimated to have the lowest fuel operating cost at just $0.003 /tonne-km. The hauling method with the highest operating cost not including fuel cost is estimated to be long haul diesel trucks at $0.069 /tonne-km. The lowest non-fuel operating cost is estimated to be Railveyor at $0.005 /tonne-km. Section 2 (Haulage Analysis) of this report details the method of calculations and sources for the energy, costs and emissions factors.
The hauling method with the highest embedded (Scope 3) emissions per tonne of vehicle capacity is estimated to be the battery electric vehicle (BEV) haul truck at 2.6 tonnes CO2e/tonne vehicle capacity. This is a result of emissions associated with the production of the battery used to power the vehicle. However, it is important to note that the Scope 2 emissions during the use phase of a BEV haul truck are half that of the diesel-electric haul truck. The system with the lowest Scope 3 emissions per tonne of vehicle capacity is diesel heavy rail, estimated to be 0.36 tonnes CO2e/tonne vehicle capacity. This is a result of the material efficiency used in the rail cars, along with the high haul capacity of each vehicle.
The embedded (Scope 3) emissions associated with the infrastructure required for each hauling method is the highest for Diesel-Heavy Rail, at 941 tonnes CO2e/km of infrastructure. This high emissions factor is heavily influenced by the amount of raw material and extensive installation operations required by rail infrastructure. The lowest emissions associated with infrastructure are estimated to be gravel haul roads, the infrastructure associated with diesel haul trucks, BEVs, and hydrogen fuel cell trucks at 699 tonnes CO2e/km of infrastructure.
Apples to Apples Mine Scenario
While cost and emissions factors on a per tonne-km basis are valuable for comparative analysis, the comparison is easier to see in the context of an operation. The study team used a theoretical scenario of 10 million tonnes annually (~30k tonnes/day) and 10km. The chart below illustrates the overall ten-year total emissions per haulage option.
About This Project
This project emerged from the work performed by the study team (Warm Springs Consulting’s technical team) for the Integra DeLamar Prefeasibility Study. Over the 18 months of that project and various iterative analyses, it became evident that Railveyor had significantly lower fuel and non-fuel operating costs compared to diesel haul trucks - and perhaps other haulage systems. During the WSC and Railveyor collaboration on Integra DeLamar PFS, Railveyor inquired about developing a larger study to compare Railveyor to other haulage options. WSC’s leadership also saw a need for this type of study - as it would serve not only WSC’s work with other mining and agricultural clients, but it would provide valuable information to industries seeking pathways to net zero. This report is written for those who seek to reduce ghg emissions and costs in overland haulage systems.
The technical team at Warm Springs Consulting agreed to take on this project with some initial funding from Railveyor. Railveyor’s sponsorship covered approximately one third of the total cost to develop this study. While Railveyor’s team provided guidance, input and feedback, the company did not have editorial control over this study. The conclusions in this document are grounded in the data and calculations developed solely by Warm Springs Consulting’s technical team.
Our goal in this endeavor is to provide valuable information around potential costs and emissions of various haulage systems to decision-makers in the mining sector. The study team welcomes questions, revision suggestions, and critique. If you would like to provide feedback and technical review for this study, please contact Aly Dritenbas (aly@warmspringsconsulting.com), Business Manager and Research Coordinator at Warm Springs Consulting.
About The Study Team
The authors of this report are part of the technical team at Warm Springs Consulting, which mostly focuses on climate solutions for mining and large impact industries. As a team, we are all passionately committed to solving interesting problems - we see climate change as one of the most urgent and interesting problems of our time. We’re engineers, economists, legal experts and philosophers that think in systems and take a holistic approach to our work. As both explorers and homebodies, we love to climb mountains and curl up with a good book. We have families of all shapes and sizes. On our wall, we hang degrees, certificates, kid drawings and a photo of our next adventure destination. We’re introverts and extroverts, thinkers and feelers, and all the personalities that make up one amazing team.
Warm Springs Consulting (WSC) is an Idaho-based, internationally recognized, sustainability consulting firm that serves high-impact industries, businesses and governments by guiding clients in how to leverage sustainability as a strategic and profitable advantage. We support companies in significantly moving the needle on greenhouse gas (GHG) emissions reduction while achieving sustainable profits. Our diverse body of work covers sustainability strategy, economic feasibility studies, electrification analysis, GHG inventories, human-centered design solutions, climate resilience strategies, scenario planning, energy and waste planning, technology planning and deployment, communications, and organizational training.
To learn more about the Warm Springs Consulting Team visit: www.warmspringsconsulting.com/team
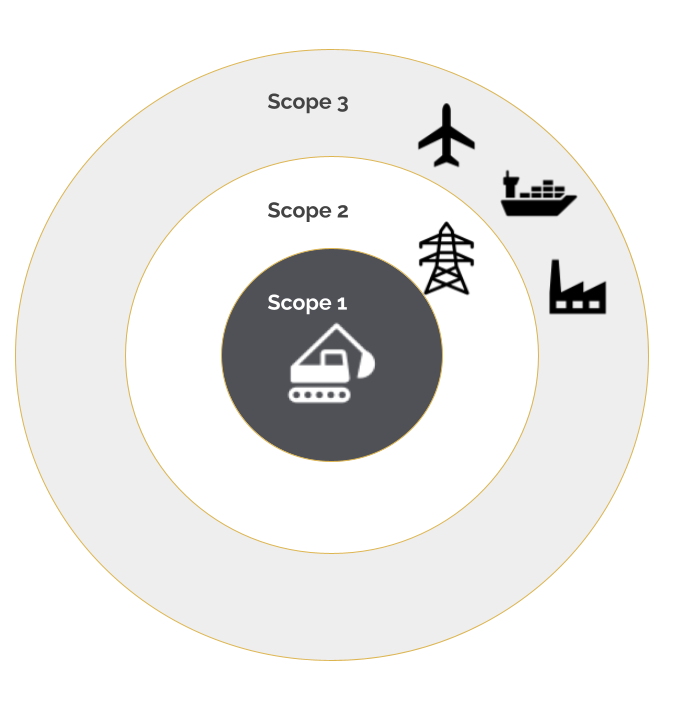
Results
Diesel-electric haul trucks are estimated to have the highest GHG emissions of the specified hauling methods at 0.096 kilograms CO2e /tonne-km. This is directly related to the high emissions factor of diesel fuel and limited haul capacity per truck. The hauling method with the lowest emissions is the Railveyor system, with an estimated 0.012 kilograms CO2e /tonne-km.
Large haul trucks have been the industry standard for over 50 years and offer flexibility, relatively low capital cost (especially with equipment lease options), and guaranteed technology with known maintenance.
The challenge will be to justify their continued use when there are more economical options that lead to significant reductions in GHG emissions.